Project successfully completed: Logistics networks in the steel industry
2025/01/17
How can steel scrap transports be bundled efficiently? Which hubs are suitable for this and what capacities are required? And how robust is the transport system in the event of disruptions or fluctuating transport volumes?
Our successfully completed research project “Logistics networks in the steel industry” examined precisely these issues. Traditionally, coal has played a central role in crude steel production, with large quantities being transported to steel producers by rail. However, climate protection requirements are setting new priorities: coal is to be increasingly replaced by hydrogen and a higher proportion of steel scrap. This change will have a profound impact on logistics: rail-based coal transportation will decrease, while scrap transportation will increase significantly. We have used simulation-based analyses to investigate these effects and identify the ideal number and placement of suitable scrap hubs.
Fewer hubs, more efficient operation? The simulation results show: A smaller number of hubs can reduce turnaround times, the number of freight wagons required and operating costs – provided that the remaining hubs have sufficient shunting capacity. However, a lean hub structure entails risks: operating costs increase in the event of disruptions, the network becomes overloaded more quickly, and train utilization and journey times deteriorate. Our analyses show that at least four hubs are necessary in the simulated transport hub to ensure robust and efficient scrap transportation.
Special thanks go to our project partner DB Cargo for the good cooperation and for funding the research project.
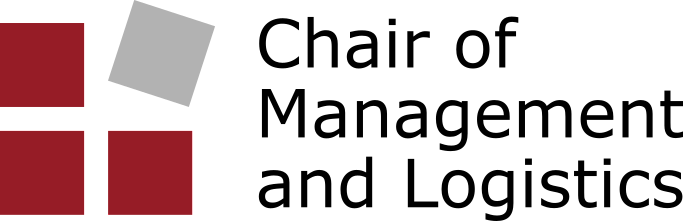