Excursion to the Mainz-Bischofsheim shunting yard
How efficient transport can function in the future is not only part of our research, but is also being investigated together with our students. As part of the “Logistics Live!” series of events and our seminar on “Transformation in transport – How does efficient freight transport succeed?”, the excursion took us to the shunting yard in Mainz-Bischofsheim.
There, 24 students gained interesting insights into the operation of rail freight transportation and its processes. The students were able to observe shunting operations at one of the most important shunting yards in the Rhine-Main region, as well as the maintenance of locomotives and freight trains. The Mainz-Bischofsheim shunting yard is one of the oldest shunting yards in Germany and one of the few that is still controlled manually. Freight trains are separated in shunting yards and assembled into new freight trains. In order to further expand climate-friendly rail freight transport in the future and make it competitive, such shunting processes must be designed as efficiently as possible. This is therefore an elementary component of efficient freight transportation in the future.
Intact equipment and shunting locomotives are also required to ensure smooth shunting operations. The students were therefore able to visit the maintenance of the shunting yard, where the shunting locomotives are repaired and maintained close to the site.
Overall, the students were able to gain exciting insights into the processes of a shunting yard and discuss the current challenges of rail freight transport with experts.
We would like to thank the hosts at the Mainz-Bischofsheim shunting yard, thanks to whose great commitment the students were able to gain comprehensive and exciting insights.
Host: DB Netz – Mainz-Bischofsheim Shunting Yard: Leo Glaubetz
Number of participants: 24 Students
Exkursion zum Railport Darmstadt der DB Cargo und Besuch der KTL Kombi-Terminal Ludwigshafen GmbH
As part of our excursion this semester, as part of the event “Logistics Live!”, 28 bachelor's and master's students from Darmstadt Technical University, who learn about current logistics problems in their studies, visited DB Cargo's Railport Darmstadt and the KTL combined transport terminal in Ludwigshafen to gain practical insights into the design of combined transport (CT) transport chains.
In the morning, the group visited the Railport near Darmstadt's main train station. The students were warmly welcomed by Jan Bellinger, the Managing Director of Railport, who showed them around the site and clearly demonstrated the challenges that have been mastered in recent years and the new concepts that have been developed and implemented. As a storage and transshipment yard, the Railport currently stores primarily cellulose rolls and spare parts for DB Cargo. Previously, the focus was on the paper industry and the chemical and construction industries. In addition, consumer goods are regularly handled for onward transport. During the tour, the students were able to experience live how the goods are reloaded in the freight cars for truck transport.
The impressions gained at Railport Darmstadt were supplemented by a visit to KTL in Ludwigshafen. There, the students were divided into two groups. While one group received information about the terminal from Harald Schlegel, the Managing Director of KTL, the other half took a bus tour of the KTL site with Michael Probst, the Operations Manager of the terminal. During the bus tour, the students learnt about the handling of intermodal transports at one of Europe's leading transshipment terminals. In addition to the process of picking up and delivering semi-trailers and containers, the students learnt about the storage and dangerous goods management at the site as well as the transshipment process between road and rail. Current challenges were also discussed, such as the differences between craneable and non-craneable semi-trailers and the preregistration of truck drivers by depositing their fingerprint in the system, which is meant to simplify the process when unloading containers and semi-trailers.
One highlight during the bus tour of the KTL site was observing the transfer of a semi-trailer to the assigned storage location with the help of a gantry crane. Here, the students were able to experience how downstream processes run and what administrative measures are necessary in the background. After about 45 minutes, the activities of both groups were switched.
All in all, the excursion to DB Cargo's Railport Darmstadt and the KTL combined transport terminal in Ludwigshafen was characterized by a very varied mix of theory and practice.
We would like to thank our hosts, whose great commitment offered the students comprehensive and exciting insights.
Hosts:
- DB Cargo AG – Railport Darmstadt: Jan Bellinger
- KTL-Kombi-Terminal Ludwigshafen GmbH: Harald Schlegel, Michael Probst
Number of participants: 28
Excursion to the Ludwigshafen combined transport terminal and BASF in Ludwigshafen
In the summer semester of 2022, our excursion to the two companies KTL (Kombi-Terminal Ludwigshafen) and BASF in Ludwigshafen, was carried out as part of the event “Logistics Live!”. Around 25 master's students from TU Darmstadt took part in the one-day excursion which included two round tours.
The first tour started at the northern most point of the extensive area in Ludwigshafen: at the KTL transshipment terminal. Here, the students learnt a lot about the operation process in one of the largest container terminals for combined transport in Europe. The main topics were warehouse management, dangerous goods management, and the handling process in the terminal. The tour continued to BASF. After a short lunch break, the students heard a company presentation of BASF. A subsequent discussion focused on the current resource shortage of gas in Germany, which is an essential materials for entire plant operations. During the second round tour, we visited all important stops of trimodal transport (road, rail, and inland waterway). The operational area for Automated Guided Vehicles (AGVs) was especially fascinating. The students learnt how AGVs (specially developed and certified by BASF) are used for self-improvement of internal logistics processes and how they offer more opportunities to increase efficiency and safeguard transport operations. We also visited the plant's internal port, where goods from inland shipping are handled.
We want to thank both companies for their extraordinary commitment and for providing the students with comprehensive and exciting insights on-site despite (still) pandemic-related restrictions!
Excursion to the Alnatura distribution center in Lorsch and a visit to BASF SE and KTL Kombi-Terminal Ludwigshafen GmbH
In the scope of Logistics Live! as part of the business management seminar at the Chair of Management and Logistics, the two excursions in the winter semester 2019/2020 brought about 25 bachelor and master students of the TU Darmstadt to Alnatura, BASF SE and KTL Kombi-Terminal Ludwigshafen GmbH.
On the first day of the excursion, the Alnatura distribution center in Lorsch was visited. After a short introduction to logistics at Alnatura by Klaus Böhmer (Head of Logistics and SCM) and team, the students went on a guided tour to the Alnatura warehouse. During the tour, the students were able to learn about the complete process from goods receipt to commissioning and goods dispatch. Afterwards, in the afternoon, the students had the opportunity to apply their knowledge in two case studies together with logistics experts from Alnatura and to present their results.
The second part of Logistics Live! brought the students to Ludwigshafen to visit BASF and the neighboring Ludwigshafen Kombiterminal (KTL). In addition to an introduction to BASF's products and projects in logistics, we had the opportunity to look at the in-house development of Automated Guided Vehicles (AGV) for improving internal logistics with the project team and visit their control center. The explanations of the BASF Class Containers, an in-house development of a tank container with a larger volume and advantageous logistical characteristics, were also very interesting. After a bus tour through the BASF premises and a refreshment in the BASF canteen “Roter Ochse”, the team then proceeded to the Ludwigshafen Kombiterminal (KTL). During a tour of the site, various aspects of KTL were explained, particularly interesting were the different ways in which intermodal transport is handled in one of the largest container terminals in Europe.
We would like to sincerely thank our hosts, Alnatura, BASF and the KTL Kombi-Terminal Ludwigshafen for the fascinating insights.
Hosts:
- Alnatura: Klaus Böhmer, Franziska Zieger
- BASF und KTL: Harald Schlegel
Number of participants: 25
Excursion to Bosch Rexroth AG in Lohr am Main and to the Daimler Global Logistics Center in Germersheim
The excursions of the Chair of Management and Logistics as part of the additional event “Logistics Live!” led this semester around 40 Bachelor and Master students of the TU Darmstadt to Bosch Rexroth AG and Daimler AG. The focus was on logistics processes in practice as well as new technologies for application in logistics.
On the first day, Bosch Rexroth was visited in Lohr am Main, one of the world's leading specialists in drive and control technology. The students were warmly welcomed by Mrs. Stienkemeier and Mrs. Falkenstoerfer, who looked after them throughout the day. After a short introduction to the company as well as the presentation of the entry possibilities for students, an exciting technical lecture was given by Mr. Salm, head of the logistics department, on the subject of forecasting (information logistics). After a refreshment in the cafeteria, a tour of the goods distribution center took place. Here the flow of material from incoming goods to outgoing goods was followed. Mrs. Kneisel-Büchner (head of department) and her team gave the students a comprehensive insight into the processes of goods distribution from Lohr to the other Bosch Rexroth locations worldwide.
On the second day of “Logistics Live!” the Daimler AG in Germersheim was visited. This is where the Daimler Global Logistics Center is located, where spare parts are stored and which is considered the largest warehouse in the automotive industry worldwide. After an exciting tour of the warehouse with Ms. Hahn, Mr. Harnischmacher gave insights into the TechLab, where innovative technologies are tested for use in the warehouse. In the subsequent presentation by Dr. Benz, the company was introduced in more detail and the possibilities for starting a career were presented. Dr. Thiel then gave an interesting presentation on the planning of IT systems at Daimler AG. Finally, Dr. Reiß gave an insight into the concept of agile working methods as well as the concrete implementation within the group.
Overall, the two excursions to Bosch Rexroth AG and Daimler AG were characterized by a very varied mix of practice and theory. Thanks to the great commitment of the participating practice partners, the students were able to gain comprehensive and exciting insights. The guided tours enabled the students to experience warehouse technology at first hand and to learn about processes in incoming goods, order picking and outgoing goods. In addition, the students were able to expand their theoretical knowledge of current challenges and methodical approaches in lectures and learn new perspectives.
Hosts:
- Bosch Rexroth AG: Mrs Stienkemeier, Mrs Falkenstoerfer, Mr Salm, Mrs Kneisel-Büchner
- Daimler AG: Dr. Thiel, Mrs. Hahn, Mr. Harnischmacher, Mrs. Dr. Benz, Dr. Reiß
Number of participants: 40 students
Field trip to the enterprises Dematic GmbH and DHL Paketzentrum Obertshausen
The tenth excursion of the Chair of Management and Logistics as part of the business management seminar gave about 25 bachelor and master students of the TU Darmstadt an insight into the practical application of advanced technology in various intralogistics processes.
The first stop was made at the intralogistics manufacturer Dematic GmbH. After the students had received a short introduction to the history of Dematic, in which even a participation of the company in the construction of RMS Titanic was admitted, they went directly to the Imagination Center. There the excursion participants could inform themselves about the three basic characteristics of an intralogistics solution “smart”, “rapid” and “flexible”. A tailor-made solution was then generated with the help of an interactive program for systematic service development. The following guided tour through the Tech Center showed how storage and retrieval is carried out using highly dynamic automated systems. In addition, the students were able to observe how products from mixed pallets are received and automatically stored, as well as follow their reassembly for dispatch. The visit to Dematic GmbH was concluded by a demonstration of the pocket sorter system and a robot arm that picks with the aid of a vacuum gripper.
After the participants of the excursion were able to get to know various solutions for intralogistic processes, they were able to see the use of the systems in operation at the second station of the excursion, which led to the DHL Paketzentrum Obertshausen. During the tour of numerous staircases, corridors and staircases artfully winding around the conveyor and sorting technology, it became clear how complex the processes in a parcel sorting centre are. Even with a now high degree of automation, people still play a decisive role and are an indispensable part of the rapid processes in the parcel sorting centre.
We would like to thank our hosts, Dematic GmbH and DHL Paketzentrum Obertshausen
Number of participants: 25
Field Trip to the enterprises Merck KGaA and LOGOSYS Logistik GmbH & Co. KG
Already for the ninth time, the Chair of Management and Logistics organized a one-day field trip in the context of the economics seminar. About 20 bachelor and master students participated in the event whose focus was on logistics processes and the special logistic challenges of the both enterprises located in Darmstadt.
On the morning of 18th January, the participants had the opportunity to get to know the logistics processes of the chemical and pharmaceutical enterprise Merck at the first stop of the trip. After being welcomed by the representatives of the enterprise, Mr. Müller (Manager Distribution Center), Mr. Abbe (Group Leader Storage and Order Picking) and Mr. Seitel (Manager Central Warehouse), the group was divided for the following tour. During the tour the student got an insight into the entire process from the receipt of goods over the central warehouse and the distribution centre including special storages for dangerous materials to the assignment and goods issuing department. Finally, during a collective refreshment the opportunity was given to discuss open questions and impressions of the tour.
At the second stop of the field trip in the afternoon, the participants were welcomed at LOGOSYS Logistik GmbH & Co. KG which is one of the most important logistics service providers of Merck KGaA. Firstly, Mr. Reinhard, the managing director of LOGOSYS GmbH & Co. KG, presented the history and business areas of the company. Thereby, especially the unique requirements on a medium-sized logistics service provider in the pharmaceutical business as well as the resulting wide range of logistics and additional operations offered by the enterprise were illustrated. After the interesting enterprise presentation the students were guided in small groups through the logistics centre by Mr. Reinhard, Mr. Diethelm and Mr. Wienholt. During the tour, the different storage areas (high rack warehouse, cold storage, picking warehouse) as well as the areas for pharmaceutical packaging were visited. Finally, the students were given the opportunity to discuss open questions.
Hosts:
- Merck KGaA: Thorsten Müller, Michael Abbe, Peter Seitel
- LOGOSYS Logistik GmbH & Co. KG: Jürgen Reinhard
Attendance: 24
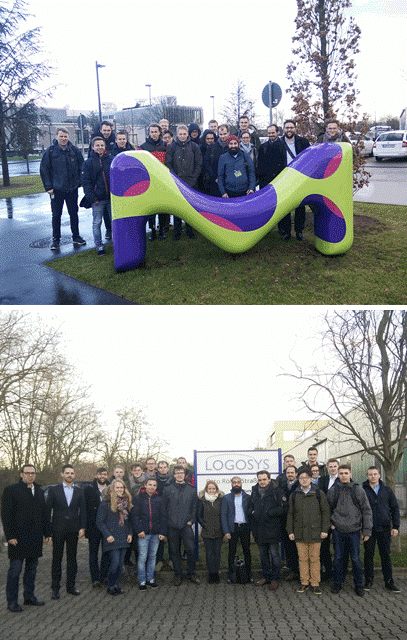
Field trip to the enterprise Dachser Logistikzentrum Karlsruhe GmbH & Co. KG in Malsch
After concluding the seminar “Virtual & Augmented Reality – possible applications and potentials for development in Logistics and Transport” in the summer term 2017, the participants and other interested students were given the opportunity to experience the use of augmented reality in practice. Hereby, the Chair of Management and Logistics offered a one-day trip to Dachser Logistikzentrum Karlsruhe GmbH & Co. KG in Malsch. The field trip was organized in close cooperation with Mr. Karheinz Klatt of Dachser SE & Co. KG. In the context of the seminar, the students worked out theoretically possible applications of virtual and augmented reality in manual order picking systems. Through the field trip this theoretic base was complemented by insights on practical applications. In several discussions, the students could contribute their questions and proposals and get to know aspects about order picking systems which are relevant for practice.
The first part of the field trip contained a guided tour through the two storehouses of the company’s site where industrial and consumer goods from most different industries are handled. Mr. Michael Knieper (Dachser Expert Warehouse Operations) explained the recent challenges regarding the demands on customer-specific order picking. The participants could experience the assisting systems pick-by-vision and pick-by-voice as well as picking by handheld terminal. In this context, Mr. Knieper illustrated the advantages and disadvantages of different technologies and gave an outlook on the recent developments in the Dachser group.
After a small lunch, Mr. Manuel Cloos (project manager, Dachser Expert Warehouse Operations) presented the company-intern pilot scheme on pick-by-vision answering rising questions of the audience. The recent status of the project and the functionality of the technology were explained in detail. Thereby, concrete challenges of the innovative picking technique were explained comprehensively and their advantages in comparison to existing assisting systems were emphasized once again. Subsequently, as a highlight of the field trip, the students were given the opportunity to test the pick-by-vision technology on their own. An illustrative picking order could be fulfilled in a simulation with augmented reality glasses and a mobile scanner. Thereby, the participant put themselves in the place of a picker and experienced the technology at first hand.
Hosts:
- Dachser SE & Co. KG: Karlheinz Klatt, Michael Knieper, Manuel Cloos
Attendance: 24
Trip to Merck KGaA and DB Cargo AG
In the winter term 2016/17 the Department of Management and Logistics organized a one day field trip for seminar participants and other students of the department as well as interested external students. The focus was on giving an insight into logistics systems of several companies and on showing up job-relevant key qualifications. About 20 bachelor and master students of TU Darmstadt who have chosen a focus on logistics studies in their curriculum participated in the event. On a freezing day in January, the students were given the opportunity to get to know the enterprises Merck and the DB Cargo Railport in Darmstadt as well as the possibility to socialize.
The first stop of the field trip led the students to Merck KGaA, an enterprise of the chemical and pharmaceutical industry in Darmstadt. First, the representatives of the enterprise welcomed the students. Mr. Müller (Director Distribution Center Darmstadt), Mr. Abbe (Group Leader Storage and Assignment) and Mr. Seitel (Manager Central Warehouse Darmstadt) explained briefly their individual professional background. After that, the group was divided for a tour through the central warehouse and the distribution centre which offered the possibility to get to know the real time logistics processes reaching from the receipt of goods and product testing over the central storage of dangerous materials, preliminary and final products to the distribution centre including assignment and the goods issuing department. By midday, both groups met again for short refreshment and the possibility to discuss their questions.
The second stop of the excursion was at DB Cargo Railport near the central station of Darmstadt. The railport, as storage and transhipment hub serving also Merck products, has been able to expand its business from a focus on paper industry to further industries (chemical or construction industry) during the last years. Mr. Langendorf (Head of Controlling, Manufacturing Centre Frankfurt) and Mr. Hörnig (Railport Manager Darmstadt) taught the students about the challenges they tackled during the past years and how they developed and implemented new concepts for the railport. Mr. Hörnig then led the group around the site. Besides gaining an interesting insight on the railport concept, the participants of the field trip were given the extraordinary opportunity to get behind the wheel of a wheel loader daring to manoeuvre the vehicle across the area.
Hosts:
- Merck KGaA: Thorsten Müller, Michael Abbe, Peter Seitel
- DB Cargo AG: Klaus Langendorf, Martin Hörnig
Attendance: 34
Two-day field trip to the companies Bosch Rexroth, MyToys and Evonik
In the summer term of 2016 the Department of Management and Logistics once more organized the two-day event “Logistics Live!”. The focus was on giving an insight into logistics systems of several companies and on showing up job-relevant key qualifications. 27 bachelor and master students of the TU Darmstadt who have chosen a focus on logistics studies in their curriculum participated in the event. During the two days the participants were given the opportunity to get to know the enterprises Bosch Rexroth, MyToys and Evonik at their sites in Lohr am Main, Gernsheim and Weiterstadt.
The first stop of “Logistics Live!” led the students to Bosch Rexroth AG in Lohr am Main, one of the worldwide leading specialists for drive and control technology. At the beginning, there was an intense exchange between students and representatives of the company. After an introduction with the company’s presentation held by Ms. Ulrich, possible career opportunities were presented in addition. Hereby, one participant of the PreMaster program (Maike Blattner – career entry in logistics after a bachelor graduation) and respectively one participant of the Graduate Specialist Program (Patrizia Schäfer – career entry in controlling with a second position in Controlling after a master graduation) reported about their own professional development and showed possible career paths in logistics. After a refreshment through a collective lunch, the logistics area of Bosch Rexroth was presented in a tour through the factory guided by logistics manager Mr. Becker. During and after the visitation the students had the opportunity to discuss with Mr. Becker about particular logistics and production processes and possible solutions for different logistic problems.
The second stop of the trip lead to the MyToys group in Gernsheim. The MyToys group includes MyToys, ambellis, mirapodo and limango whereby MyToys as number two in the online toys market holds the biggest share of the enterprise. On a tour through the firm’s storage area of more than 75,000 square metres which took about two and a half hours the students were guided in two groups by Mr. Rother (logistics manager) and Mr. Heubach (returns manager). Thus, they were able to get a broad insight into the logistic processes reaching from incoming goods over the fully automatic carton storage as well as the handling of small and big parts to the national and international goods shipping. In advance, possible career opportunities at MyToys were presented by Ms. Michel (human resource representative) and finally Mr. Rother gave exciting insights on the company’s KPI and challenges which are especially connected to the Christmas and Easter business at MyToys.
The last stop of the trip was at Evonik in Weiterstadt. After being welcomed by Mr. Görg (manager corporate community corporation), Dr. Neher (site manager) held a presentation about the worldwide leading enterprise for specialty chemicals and its sites in Darmstadt and Weiterstadt. After that, Mr. Ihnen (logistics manager Rhine/Main) and Mr. Drönner (operative logistics manager) introduced the students to the diversity of logistics at Evonik. After a motorized tour through the plant Mr. Vogel (logistics centre manager) guided the participants for one hour through the logistics centre for acrylic glass and gave fascinating insights into logistics at Evonik.
Field Trip to DB Schenker, Siemens and Kirow
The focus during the two-day field trip “Logistics Live!” in the winter term of 2015/16 which was organized by the Department of Management and Logistics was on giving an insight into logistics systems of various industrial enterprises and on showing up key skills which are relevant on the job. Taking place for the fifth time, the event offered 28 students the opportunity to get to know DB Schenker, Siemens and Kirow as well as the possibility of socializing. The students were able to get to know the field of action of a logistics manager in different enterprises and branches of trade capturing impulses for their own professional orientation.
The first stop of the trip was the Siemens combination engineering plant at Chemnitz. The plant which started its work in 2014 is a production facility for the installation of electric control cabinets but also for the production of machine tools, producing machines, conveyor techniques and other customer specified products. The customer specified completion of the cabinets causes extraordinary requirements for logistics and supply chain management. To fulfil the customers’ needs more than 10,000 single components have to be ordered, stored and handed over for installation at the right time.
Arriving at Chemnitz the participants were welcomed by Mr. Kocarnik, the logistics manager of the production site, and were provided drinks and food. After a presentation about the traditional history of the production site as well as about details of the products and daily challenges of logistics on the site the students got the opportunity to take a look at the production facilities including different installation places and warehouses. Thereby, the tight and complex networking of logistics service providers and producing enterprises was very striking being essential for an unobstructed and efficient operating schedule. To get a deeper insight into the work of a logistics service provider on-site the next stop of the field trip was the nearby distribution center of DB Schenker.
The second day of the field trip began with a visit of a further facility of DB Schenker. This time the students were given the possibility to get a picture of the distribution center at Leipzig which is especially occupied with the production supply of international automobile factories. In contrast to the previously visited office in Chemnitz the participants were given the chance to compare different challenges of logistics differentiating between the needs of different lines of business.
The fourth stop of the field trip lead to Kirow/Kranunion GmbH at Leipzig.
Visiting a medium-sized enterprise with a focus on the development and production of railway cranes another activity field with further logistics tasks could be experienced. Due to its impressing size but also because of the variety of products, further interesting production and logistics processes were explained in such a way that it was very well understandable. The detailed and exciting tour through the different installation and production facilities guided by Mr. Ehmisch showed the students how variegated and challenging the work in a medium-sized enterprise is and how much high-tech and know-how is needed to develop and produce a safe and robust railway crane.
Hosts:
- Siemens AG: Herr Kocarnik
- DB Schenker: Frau Afsaoui, Frau Bachmann, Frau Göckeritz, Herr Dr. Tran
- Kirow/Kranunion GmbH: Frau Schneider, Herr Ehmisch
Attendance: 28 students
Two-day field trip to the companies Adam Opel AG, DB Schenker and Bosch Rexroth AG
In the summer term of 2015 the Department of Management and Logistics again organized the two-day event “Logistics Live!”. The focus of the trip was to gain valuable insights into the logistics divisions of different companies (OEM, first-tier supplier and logistics service provider) and to learn more about job-relevant key qualifications. 35 bachelor and master students of the TU Darmstadt who put an emphasis of their studies on logistics attended the event. Over two days the participants had the opportunity to get to know the companies Adam Opel AG, DB Schenker and Bosch Rexroth AG at the locations Rüsselsheim, Rodgau and Lohr am Main. Furthermore, they got the chance to make contacts to the practice partners on the management level. Thereby, the students were able to experience the fields of activities as well as the duties of logistics managers and capture impulses for their own professional orientation.
The first stop of “Logistics Live!” was the tradition-rich production site Rüsselsheim of the Adam Opel AG. This location can look back on 150 years of traditions. Today, mainly the two models Insignia and Zafira leave the production line at this plant. After a welcome from Mrs. Schad (HR Talent Acquisition) in the Adam Opel House, the students got the opportunity to take part in a tour through the production plant. They followed the whole process of car manufacturing, starting in the classic and vintage car workshop. From there, they visited the pressing plant, the car-body construction and followed the cars till their final assembly. In a following presentation Mr. Scholl (Director Opel / Vauxhall Supply Chain) impressively illustrated the students what the challenges of their supply chain are. Thereby, he presented topic “Order Slotting”, which is a new process concerning real-time order processing by comparing available stock. This demonstrated how the collaboration can significantly be improved by digital, cross-functional implementation of new processes. In February 2015 Opel was rewarded for their new Order Slotting process by the VDA (Verband der Deutschen Automobilindustrie). Afterwards the students were invited to join a Job-Speed Dating, where they were able to ask the four directors and six managers of the divisions SC Planning, SC Operations Europe, SC Order Fulfillment and SC Logistics Europe in small groups target-specific questions.
The second stop of the trip was the Logistics Operations Excellence Center (LOEC) of DB Schenker in Rodgau. DB Schenker represents the business field of transportation and logistics of Deutsche Bahn und is one of the world’s largest transportation and logistics service provider. As one of the few LOEC at DB Schenker, the warehouse in Rodgau is an outstanding example for the integration of lean management standards and the implementation of continuous improvement processes in the area of warehousing.
Right at the beginning Mr. Dr. Tran (Research and Innovation Management) introduced DB Schenker and gave the students an idea of the company. Following the presentation, a highlight was the guided tour through the high rack warehouse. During this conclusion of the first day the processes in the warehouse were explained to the students in a very illustrative way.
This year the students traveled for the third station of the event “Logistics Live!” to the headquarters of Bosch Rexroth AG in Lohr am Main. Bosch Rexroth is one of the leading specialists for drive and control technologies. Again the focus of the visit at the plant was the intensive exchange between the representatives of the company and the students. After Mrs. Güther (Employee Marketing and Talent Management) started with a presentation about the company, the logistics plant manager, Mr. Lindemann, introduced and explained the logistics division at Bosch Rexroth in more detail. He guided the students for an one-hour tour through the plant. During and after the tour the students had the chance to ask Mr. Lindemann questions about the different processes, from the arrival of incoming goods to the fully automated high rack warehouse, the production line and the shipment of goods. Moreover, they were able to discuss solutions for logistical problems with Mr. Lindemann.
After all participants were invited for lunch, the career options at Bosch Rexroth were presented. In this context a member of the PreMaster Program (entry with a bachelor degree) and a member of the Graduate Specialist Program (entry with a master degree) talked about their development and showed the students possible directions for careers in the field of logistics.
Hosts:
- Adam Opel AG: Julia Schad, Michael Scholl, Marzell Bandur, Peter Ludwig Deuer, Andreas Graffe, Andreas Ginkel, Arne Sell, Michael Gorny, Andre Dammel, Miriam Wolak, Julia Kennel, Matthias Hecker
- DB Schenker: Dr. Chung Anh Tran, Ralf Schröder, Marion Müller
- Bosch Rexroth AG: Maria-Luise Güther, Dr. Eckhard Lindemann, Alexander Lintl, Michael Albers
Attendance: 35 students
Field trip to BMW AG, Continental Automotive GmbH and Schenker Deutschland AG
The Chair of Management and Logistics organized the two-day event “Logistics Live!” in the winter term 2014/2015 in Regensburg. The main objective was to gain insights into the logistics operations of various companies (OEM, 1-Tier Supplier and Logistics Services Provider) and the presentation of career-relevant soft skills. 35 students participated in the event and used the opportunity to get in contact with industry partners from the management level of the three companies BMW AG, Continental Automotive GmbH and Schenker Deutschland AG in Regensburg, Germany. The students were able to get insights into the profession and typical activities of a logistics manager and got impulses for their future career.
Hosts:
- BMW AG: Frau Fuchs, Frau Berger (Monocom GmbH), Herr Politzka
- Continental Automotive GmbH: Herr Hymon, Frau Frey, Frau Fischer
- Schenker Deutschland AG: Herr Wutz
Number of participants: 35 Students
Additional photos:
Field trip to BASF SE headquarters at Ludwigshafen including a visit at the KTL Kombi Terminal Ludwigshafen GmbH, Terminal Frankfurt/Main-Ost at the Deutsche Umschlaggesellschaft Schiene-Straße (DUSS) mbH and the headquarters of TFG Transfracht mbH in Frankfurt/Main
The focus topic of the 2-days field trip in the summer term 2014 was combined transport. The goal was to show the students in the field how combined transports are working, which potentials and advantages they have as well as which challenges actors in the transportation chain are facing. On the first day the 23 students had the opportunity to learn more about the interface of the transport carriers road and rail at the BASF headquarters and the KTL Kombi terminal in Ludwigshafen. On the second day the students visited the terminal Frankfurt/Main-Ost of the Deutsche Umschlagsgesellschaft Schiene-Straße (DUSS) and the headquarters of the TFG Transfracht in Frankfurt. That way the students had the opportunity to get in contact with four different enterprises which are working as combined transport, terminal and rail operators. The students could experience various fields of activity at the different enterprises and gather impulses for their future job orientation.
Hosts:
- BASF SE, Ludwigshafen: Mr. Rogge
- KTL Kombi-Terminal Ludwigshafen GmbH: Mr.Klein, Mr. Lein
- DUSS mbh, Terminal Frankfurt: Mr. Barbi, Mrs. Gruhn
- TFG Transfracht mbh, Frankfurt: Mr. Babakoudis, Mr. Engel
Participants: 23 students
Field trip to AUDI AG, Bosch Rexroth AG and DB Schenker
The main objective of the two-day event “Logistics Live!” in the winter term 2013/2014 of the Department of Management and Logistics was to gain insights into the logistics of various companies (OEM, 1-Tier Supplier and Logistics Services Provider) and the presentation of career-relevant key skills. The event which was offered in this form for the first time gave 36 students the opportunity to meet and make contact with industry partners from the management level of the three companies AUDI AG, Bosch Rexroth AG and DB Schenker AG. The students were able to get practical insight into the activity fields of a logistics manager and gain impulses for occupational orientation.
Hosts:
- AUDI AG: Mrs. Schäfer, Mr. Schröer
- Bosch Rexroth AG: Mrs. Stiasny, Mr. Becker, Dr. Simon
- DB Schenker: Dr. Tran, Mrs. Afsaoui, Mr. Pulko, Mr. Treutler, Mr. Schröder, Mrs. Müller
Participants: 36 students
Additional Photos:
Seminar Field Trip to Deutz AG, Duisburger Hafen AG and Evonik Industries AG
The focus of the seminar at the Department of Management and Logistics in the summer term 2013 was logistics services engineering. In this context, students elaborated and presented the different aspects of the topic, such as outsourcing, tender management, controlling, inventory management and combined transport. The theoretical subject area of product and process innovations in transportation and contract logistics were experienced practically by more than 30 students and the department team during a two-day seminar field trip to Deutz AG, Duisburg Hafen AG and Evonik Industries AG.
Hosts:
- Deutz AG: Mr. Männche , Dr. Binder, Mrs. Kautz, Mr. Rudolf
- Duisport-Group: Dr. Böcker, Mr. Mut, Mr. Franke
- Evonik Industries AG: Dr. Merath , Mr. Nahler , Mrs. Janosch, Mrs. Letterhaus , Mr. Naumann
Number of participants: 34
Additional Photos:
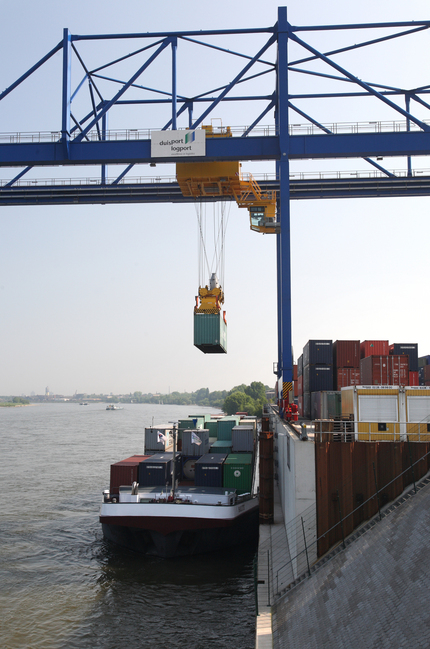
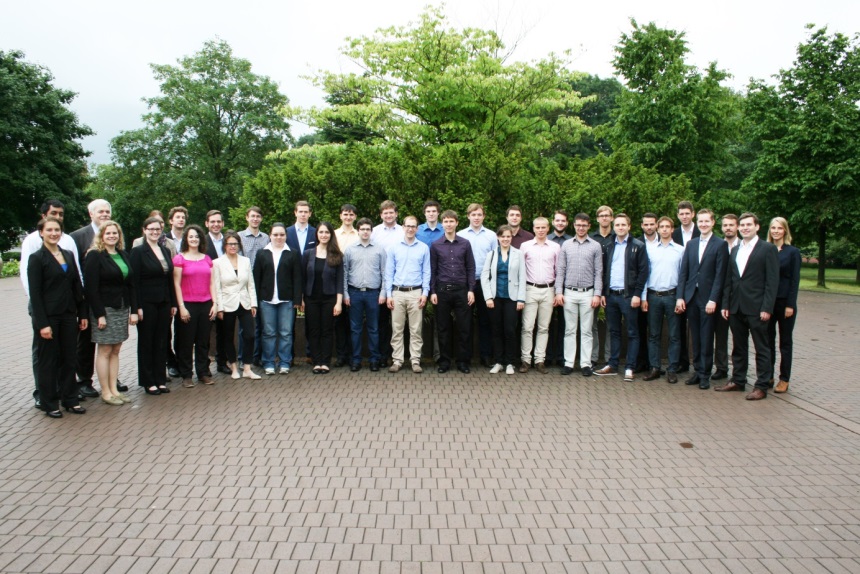
Seminar “Internationales Management – Successful Management of International Companies”
In the winter term 2012/2013 the business administration seminar covered the management of international companies. In the seminar papers the students dealt with various aspects of international management with a focus on German small- and medium-sized enterprises for machine and plant manufacturing. During the seminar the analysis of potential markets, the organizational requirements for the various forms of market cultivation, product design and the presentation of the product at fairs were discussed. The challenge in managing international teams and employee delegation as well as the need for intercultural competence were discussed as well. The seminar was organized in collaboration with the Association of German Engineering Federation (VDMA).
Hosts:
- SKF GmbH: Mr. Bastian Mattlener (HR Marketing), Mr. Peter Scharnberger , Mr. Thomas Helfrich , Mr. Ingo Wellmann and Mr. Jean-Philippe Clauvelin
- MULTIVAC Sepp Haggenmüller GmbH & Co. KG: Mr. Hans-Joachim Boekstegers (Chairman of the Board), Mrs. Rebecca Foth (Assistant to the Executive Director) and Mr Frank Gabriel (Executive Assistant)
- ESTA Apparatebau GmbH & Co. KG: Dr. Peter Kulitz (Managing Partner), Mr Jürgen Gast (Board Member, Sales & Marketing Manager) and Mr. Philip Raunitschke (Member of the Executive Board, Head of Operations/Administration & Finance )
Participants: 32 students
Additional Photos:
Seminar “The future of international transport chains”
Field trip to Hamburg at the container terminal Altenwerder, the Hamburger Hafen und Logistik AG and the corporate headquarters of Hapag-Lloyd AG Deutschland
In the summer term 2012 the seminar was covering current and future developments in international transport chains focusing on the maritime transport chain. Topics ranged from the study of current trends in decarbonizing and competition between container ports to the development of new business models for the actors involved in the transport chain. Furthermore, analyses of statistical forecasting models for container handling and simulation of container handling at on-dock rail terminals were examined.
As part of the seminar field trip the Hamburger Hafen und Logistik AG and the Hapag-Lloyd AG were visited in Hamburg. Students had the opportunity to experience the processes on the highly automated container terminal Altenwerder. Through the presentations of the hosts of both companies the seminar was supplemented with valuable insights into the latest developments in practice. Finally, a lively discussion based on the presentations emerged between the experts and the students.
Hosts:
- Mrs. John (Head of the department terminal development, HHLA)
- Mr. Hirt (Head of policy dialogue and business development, HHLA), Mr. Stieper (Head of Operations, Hapag – Lloyd)
Participants: 30 students
Seminar “Management of Robust Distribution Systems”
Field trip to Metzingen Hugo Boss
In the winter term 2011/12 the Department of Management and Logistics conducted a seminar on the topic “Management of Robust Distribution Systems”. Thereby 32 students elaborated 13 different tasks related to sustainable distribution systems and mega trends in logistics. After a discussion of the interim results, the final results were presented in two days. A highlight was the first presentation, which took place at Hugo Boss in Metzingen. In addition to a presentation of the company, its history and the current logistics projects, the visit of a central hanging garment warehouse was definitely a highlight for the students. However, the extensive discussions and background information during presentations of the seminar papers are particularly noteworthy.
The experts gave immediate feedback to the presentations, to the contributions to the discussion and information from the logistic daily routine. So the students achieved broad insights from hands-on experts during the seminar. With the help of Hugo Boss the students were able to gain an understanding of the currently implemented logistics solutions.
Hosts:
- Hugo Boss: Mr. Schneider (Director Global Logistics), Mrs. Münzing (Head of Logistics Project Management), Mr. Jender (HR Manager ), Mr. Leibfritz (Head of Logistics Planning)
Participants: 32 students